First, the danger of cable water
In general, power cables are not allowed to enter the water during production. The inside of the cable must be dry. Because of the harsh electric field voltage test, the incoming cable cannot be shipped.
Once the cable enters the water, under the action of the electric field, water tree aging will occur, which will eventually lead to cable breakdown. Water trees are a collection of voids filled with water from 0.1 m to several microns in diameter. The local high-electric field formed by the impurities, pores and insulation in the insulation and the unevenness of the bonding surface of the inner and outer semi-conductive layers is the starting point of the water tree. The development process of water trees is generally more than 8 years. The higher the humidity, temperature and voltage, the more ions are contained in the water, the faster the water tree develops.
The water directly enters the low-voltage power cable, causing corrosion of metal such as steel strips and copper strips, and the insulation performance is degraded. When water passes through the insulation, it will cause cable breakdown and even explosion and injury.
Second, the reason for the cable water
(1) At the time of storage
The newly purchased cable-forming cable is sealed with a heat-shrinkable plastic sealing sleeve at both ends. After the user has used it for a while, the remaining one is wrapped with plastic paper and tied with a rope outside. The sealing is not good, and the time is long. Water vapor will seep into the cable.
(2) When laying cables
When the cable is laid, the cable head wrapped with plastic paper is sometimes immersed in water to allow water to enter the cable; when pulling and pipe-piercing, the outer sheath rupture sometimes occurs, causing water to enter the cable.
(3) After laying
After laying, the cable head is not made in time, so that the unsealed cable port is exposed to the air for a long time, even immersed in water, so that the water vapor enters the cable in large quantities.
(4) When making the cable head
At the time of cable heading (including the terminal head and the intermediate joint), the cable ends sometimes slip into the cable well with water accumulation due to the manufacturer's intention.
(5) When the cable is running
During the operation of the cable, when a fault occurs in the middle joint breakdown, the water in the cable well enters the cable along the gap; at the construction site, the external force causes the cable to break or break down, and the cable may also enter the water. Third, the power cable water treatment countermeasures
It is very difficult to dry the cable after it enters the water (such as blowing with hot nitrogen), and generally there is no corresponding equipment. In actual operation, if the cable end is filled with water, only the front end is cut a few meters. If the entire cable has been filled with water, it is not desirable and can only be scrapped. Therefore, the prevention of cable water ingress should be based on prevention, mainly using the following measures:
(1) The cable ends shall be sealed and sawn off by the end of the cable. Whether it is stacked or laid, it shall be sealed with plastic (using a special sealing sleeve for the cable) to prevent moisture infiltration.
(2) Make the cable head in time after the wire is laid.
(3) When purchasing a cable, you must select a manufacturer with excellent quality.
Since impurities, pores, etc. in the insulation are the starting point of the water tree, the quality of the cable is critical to prevent water tree aging.
(4) Strengthen the management of cable head manufacturing process
Once the cable enters the water, the earliest breakdown phenomenon is often the cable head, so the wire head is made well and can extend the overall life of the cable. If the cable is peeling off the semiconductor layer, a few traces are made on the semiconductor layer, and then the semiconductor is stripped like sugar cane peeling. However, when using a knife, if it is drawn too far, it will damage the insulation layer and bring opportunities for the generation of water trees. In addition, in the soldering, because the power can not be found, the torch will be directly used to melt the solder. At this time, the flame will damage the copper shielding layer and the insulating layer, so this phenomenon should be eliminated. The correct way to configure the UPS is because the solder The time required is generally only 10 minutes, but the power is only 500W.
(5) Using cold shrink cable head
The cold shrinkable silicone rubber cable accessory is simple and convenient to manufacture, without the need for a blowtorch or solder. The silicone rubber cable accessory is elastic and tightly attached to the cable, which overcomes the shortcomings of the heat-shrinkable material (the heat-shrinkable material has no elasticity, and there is a gap between the cable body and the cable body during the thermal expansion and contraction of the cable, which is Convenient for the development of water trees).
(6) Long cable adopts cable branch box
Such as several long cables, each of which is about 3km in length. For such cables, in addition to the intermediate joints, one or two cable branch boxes can be used. Once one of the cables enters the water, it will not spread to other segments. Cables, and also facilitate segmentation in the event of a cable failure.
(7) 8.7/10kV cable in 10kV system
This grade cable has an insulation thickness of 4.5 mm, while the 6/10 kV grade cable has an insulation thickness of 3.4 mm. Due to the increase of the thickness of the cable insulation, the field strength is reduced, and the aging of the water tree can be prevented. At the same time, since the l0kV neutral point small current grounding system is grounded in single phase, the cable must withstand a phase voltage of 1.73 times and operate as required. 2h, therefore, it is necessary to thicken the cable insulation.
(8) PVC plastic double wall corrugated pipe
The tube is corrosion-resistant, the inner wall is smooth, and the strength and toughness are good. Therefore, when the cable is directly buried, the damage of the outer sheath of the cable can be greatly reduced.
(9) Design of cable trench (tube) and cable well
Due to the limitation of conditions, the general cable laying is in the form of direct burial or cable trench, and it is directly buried. The south belongs to the coastal rainy area, and the cable trench or cable well has accumulated water for many years. Since the depth of the cable trench or cable well will exceed the depth of the sewer, drainage is difficult, so coordination should be made during planning to facilitate drainage of the cable trench (well). If the cable well is not able to accumulate water, the intermediate joint in the cable well should be supported by the bracket.
In addition, there are many chemical companies in the heavy chemical industry. During the inspection, it was found that some of the wires in the cable trench near the chemical plant were severely deformed. Therefore, the cable trench near the chemical plant must have perfect drainage facilities. In addition, when designing the cable duct, it should be as straight as possible to reduce the elbow and make the cable easy to lay. At the same time, when the cable well is made, it is divided into a large cable well and a small cable well. The large cable well can be used to pull cables and coils. As a middle joint, and in the middle of the road, where it is not convenient to make a wire well, but there must be a corner, change to a small cable well, which is used to place the diverting pulley only when laying the cable.
(10) After the test cable head of the cable is completed
Before the operation, do a high-voltage DC leakage test. In the future, only the substation cable will be pre-tested, and other cables will not be tested. Because, once the substation cable is faulty, the short-circuit current will have a great impact on the substation equipment. Therefore, if there is a problem with the electric line, it is necessary to strengthen the operation management and timely exchange.
The author believes that the post-processing of the cable fault, and the cable that is found to be faulty after the cable test, are equally troublesome to handle, and it is necessary to find the fault point and even change the cable. The shortcoming of the former is: unplanned power outage; the short-circuit current impact advantage is: no test can extend the life of the cable (some cable tests are not ideal, but can still run for a long time, and the cable test will increase after the DC test The possibility of wearing), the point of failure is obvious, easy to find. The advantages and disadvantages of the latter are exactly the opposite of the former.
Therefore, for cable users who do not test, focus on their power supply reliability. For example, the 10kV switch station that supplies power to the user uses dual power supplies to realize dispatch automation. Once one incoming cable fails, it will switch to another cable. powered by. In fact, in the new "Procedure Test Procedures for Power Equipment", the DC voltage withstand test is no longer prescribed for the cross-linked cable, and only the insulation resistance is measured, thereby simplifying the preventive test of the cable.
Smart BMS
If you want to avoid frequent battery replacement, what you need to consider is the battery lifespan. The right battery cell is the first thing to take into consideration. Compared with other batteries, the lithium iron phosphate battery cell has a longer life. The LiFePO4 battery cell owns the characteristics of high energy density, long cycle life and high safety. The cycle life of a long-life lead-acid battery is about 300-500 times. But the lithium iron phosphate power battery which build with LiFePO4 battery cell has a cycle life of more than 2000 times, which can make you can use the battery with greater peace of mind.
Multiple BMS Function
- Overcharge protection
- Over discharge protection
- Over current protection
- Temperature protection
- Short circuit protection
- Charging balance function
- Cell capacity estimation function
What is a UFO BMS equipped with?
- RS232/RS485 Communication Interfaces
- LED Indicators
- Memory Function
- Dry Contact Function (optional)
- LCD Display Function (optional)
- Total Capacity Function: Total discharge capacity Ah and total discharge energy Wh
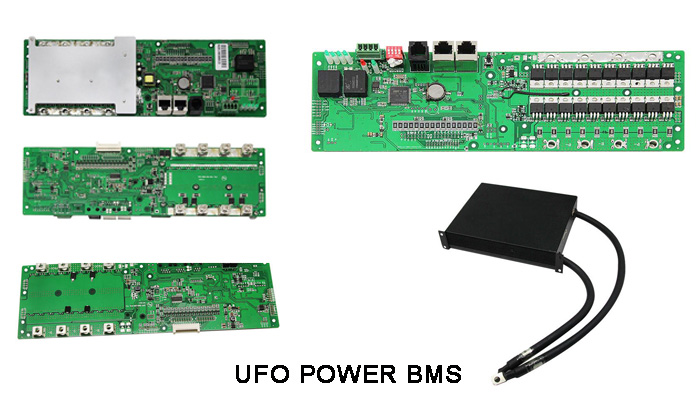
The Function of Communication Interface
â— RS232 Communication Interface
BMS can communicate with the host computer through the RS232 interface, so as to monitor the battery information at the upper computer terminal, including battery voltage, current, temperature, state, SOC, SOH and battery production information, etc.
â— RS485 Communication Interface
With RS485 interface, when the LiFePO4 Battery Pack is used in parallel, the main battery pack communicates with the slave battery ack through RS485 communication interface,so all the battery pack information can be viewed through the RS232 on the main Pack.
Smart Bms,Battery Management System,Bms For Battery,Bms For Lithium Battery
ShenZhen UFO Power Technology Co., Ltd. , https://www.ufobattery.com