In recent years, through the adoption of a new water slurry coating process and protective film technology, the powder layer process of compact fluorescent lamps in China has made breakthrough progress. As long as the domestic rare earth phosphor with good quality is used, the initial luminous flux of the lamp and the lumen maintenance rate of 2000h and 5000h can reach the current international advanced level. After China's accession to the WTO, it will further promote the export of compact fluorescent lamps. But we can't be satisfied with the status quo, but we must constantly deny ourselves, technological innovation, and occupy the world market with better products. This paper mainly discusses the process principle and technology of new water slurry coating, introduces the performance of key materials for water coating liquid in coating powder, and provides theoretical basis for formulating process specifications.
Principle of water slurry coating process
The so-called water slurry coating method is to use deionized water (or distilled water) instead of the traditional butyl acetate as a solvent, water-soluble high-water molecular polymer instead of the traditional nitrocellulose as a binder to prepare the phosphor suspension A method of applying a liquid to a phosphor layer. Unlike organic suspensions, since water is a polar solvent, particles in a suspension of water often carry opposite charges. The oppositely charged particles will attract each other due to electrostatic forces, causing flocculation of the suspension, which results in a phosphor that is less smooth and somewhat hairy. In order to prevent the flocculation of the suspension, a surfactant should be added to the suspension to change the surface characteristics of the particles in the suspension, so that they are charged with the same charge to avoid flocculation of the suspension, and a stable and well-dispersed water slurry is obtained. Apply liquid.
The aqueous slurry is composed of the following materials: phosphor, deionized water (or distilled water), temporary binder (water-soluble organic polymer), permanent reinforcing agent (alumina), surface active Agents (dispersion, wetting and defoaming agents) and pH adjusters. Dissolve the water-soluble binder into water, disperse the reinforcing agent into water, and mix the phosphor with a certain ratio, and add a surfactant. After a certain period of stirring, add a pH adjuster to make the powder. The pH of the slurry is adjusted to the isoelectric point (the isoelectric point of a dispersed particle indicates the pH value of the particle suspension, and at this pH value, the migration rate of the particle suspended in water in the electric field is zero) So that the solid particles (phosphor and inorganic reinforcing agent particles) in the slurry are charged with the same electric charge, which makes the phosphor and reinforcing agent particles disperse well in the water-coated powder slurry, and finally constitutes a stable suspension. liquid. Applying a slurry of uniformly suspended phosphor powder to the inner surface of the glass tube, drying it by hot air and baking at a high temperature to decompose and bake the temporary binder, and finally obtain a layer on the inner surface of the glass tube. Thickness of phosphor coating. If the phosphor is well dispersed in the slip, the phosphor coating is smooth, uniform, dense, and has a small porosity.
Key materials for the process
Water soluble organic polymer
Since the glass tube of the compact fluorescent lamp has been pre-bent shape, if the temperature of the baking tube is too high (6000 ° C) after coating, the glass tube will be deformed. Therefore, the temperature of the baking tube should not be too high, generally about 5500 °C. In order to obtain a phosphor powder layer without residual organic binder at a baking tube temperature of about 5500 ° C and poor air blowing conditions, the decomposition temperature of the polymer is required to be low, and the material is required to be high in monomer decomposition type. Molecular resin. Secondly, since the cerium oxide in the rare earth phosphor is an amphoteric oxide, the trivalent cerium ion will be partially dissolved in water, and the trivalent cerium ions dissolved in the water will crosslink with the ionic polymer, resulting in a suspension gel. Condensed. Therefore, the polymer used is required to be nonionic. Based on the above considerations, it has been found that polyethylene oxide is a suitable water-soluble binder. Polyethylene oxide is not ionized in water, and its aqueous solution is non-ionic; polyethylene oxide has a low decomposition temperature (decomposition starts at around 2000 ° C), and when it reaches the decomposition temperature, it decomposes from the polymer into a monomer, and these monomers The gaseous way ran away. Therefore, polyethylene oxide has been used as a binder material in the production of compact fluorescent tubes. At present, most of the domestic use is polyethylene oxide produced by Union Carbide Corporation under the designation Polyox. However, in the production of such a binder, a catalyst such as an organic compound of a metal such as calcium, zinc or aluminum is used, and these catalysts inevitably enter the finished binder to constitute impurities in the binder. If the Polyox contains CaCO3 and SiO2 impurities, the glue made of Polyox resin is opaque, flocculated and slightly yellow. According to the U.S. patent, CaCO3 and SiO2 should be separated by centrifugation. Otherwise, SiO2 and CaO will remain in the powder layer in the form of ash. Since the loading characteristics of SiO2 and CaO and HgO are very different, HgO will be adsorbed on the surface of SiO2 and CaO to form a light absorbing film, which will increase the light decay of the lamp. Therefore, the Polyox grade is not the best choice. Internationally, low-ash polyoxyethylene is catalyzed by a highly active catalyst. The amount of catalyst used is small, and the amount of impurities entering the finished binder is low. The molecular weight of this polyethylene oxide is similar to that of Polyox, and the glue prepared by it is transparent. Obviously, the use of this polyoxyethylene blending can ensure that very little impurities remain in the powder layer, and the long-term lumen maintenance rate of the lamp tube is improved.
Nano-alumina
Since we use a non-ionic water-soluble binder, in order to prevent flocculation problems, an ionic surfactant should be placed in the suspension. Even after doing so, the suspension is slightly flocculated, at which point the phosphor coating has a porosity that is better than when butyl acrylate is used or when ionic water-soluble binders (such as PVM/MA and PAA) are used. The water slurry should be large when it is coated, and the appearance is not so smooth and flat. To this end, we add high-purity (fluorescence-grade), ultra-fine (sub-micron-sized) alumina to the suspension to make the phosphor layer smooth and flat, so that the powder layer emits light evenly, so that the phosphor particles are between and fluorescent. The adhesion between the powder particles and the glass is strengthened to function as a reinforcing agent. In addition, since the loading characteristics of alumina are very similar to those of HgO (only worse than Y2O3), HgO is difficult to adsorb on the surface of AL2O3, which prevents the formation of a black light absorbing film due to the adsorption of HgO on the surface of the phosphor layer. The light attenuation of the layer is small. Another effect of the addition of alumina is the so-called "protection" effect. Since the ultrafine alumina is filled with the gap between the phosphor particles, the penetration of mercury into the glass and the thermal diffusion of sodium from the inner surface of the glass tube to the phosphor powder layer are prevented to some extent, thereby slowing down the blackening process of the glass tube glass. The formation of black sodium amalgam on the phosphor layer reduces the light decay of the lamp. Although alumina does not emit light, due to its high purity, it absorbs little ultraviolet light and visible light. Therefore, the addition of alumina does not affect the visible light emission of the lamp.
At present, the alumina powder used in China is nano-scale alumina produced by Degussa-Huls, Germany. It is produced by high-temperature hydrolysis of aluminum trichloride in an oxyhydrogen flame: 4AlCl3+6H2+3O2->2Al2O3+12HCl
Since aluminum chloride is easily purified by distillation, the by-product hydrogen chloride of the reaction is easily separated (for most applications, residual traces of hydrogen chloride are not harmful). Therefore, the purity of alumina produced by the high-temperature hydrolysis reaction is higher than that produced by the liquid phase reaction, and the particle size is small and the dispersibility is good. Germany's Degussa-Huls Company supplies γ-phase alumina to China as a fluffy white powder with hydrophilicity. Its average primary particle size is 13nm, the particles have no angularity, the BET specific surface area is 100+15m2/g, and the density is 3.2g. /ml  shaking density is about 50g / l, burning weight loss (10000C, 2h) <3%  Al2O3 content> 99.6%  SiO2 <0.1% Fe2O3 <0.2%  TiO2 <0.1%  HCl <0.5%.
Surfactant
As described above, in order to stabilize the aqueous phosphor suspension using the nonionic water-soluble binder, it is necessary to add an ionic surfactant to the suspension. The degree to which solid phase particles agglomerate into agglomerates depends on the Van derWalls attraction of the London dispersive force between the particles, which depends on the surface chemistry and load density of the solid particles. The effect of adding a surfactant to the aqueous suspension is that the surfactant changes the surface chemistry of the solid phase particles, thereby altering the interaction between the dispersed phase solid particles.
There are several basic mechanisms for affecting the surface chemistry of dispersed solid particles by adding surfactants. The simplest is to have the same charge on the surface of the dispersed phase particles. Based on the principle of homosexual repelling, the particles are kept uniform in water. Dispersion; secondly, the surface of the dispersed phase particles is oriented to adsorb a high molecular weight polymer (the molecular weight is too high or too low). The soft hydrophilic chain of this type of polymer will extend into the water and the other end will anchor to the solid phase particles. Thus, the surface of the dispersed phase solid particles is surrounded by such a high molecular polymer. When the dispersed phase particles are close to each other, the free energy of the polymer will rise and the system will be unstable. Therefore, the dispersion system can be stabilized by the "steric steric effect". It can be seen from the above two mechanisms that the added surfactant can have the above two functions at the same time, that is, the intersection of the above two mechanisms, that is, the electrostatic steric hindrance (Electrosteric) is stable, that is, the dispersed phase The surface of the particles adsorbs a negatively charged polymer. Studies have shown that the electrostatic steric hindrance mechanism minimizes the amount of surfactant required to disperse particles in water.
Since different dispersed phase particles have different isoelectric points, different acid and alkalinity, different sizes, shapes and surface properties, the type of surfactant should be selected, and the amount of addition should be reasonable.
Preparation of new water slurry powder
It can be said that the key to the new water slurry coating process is the preparation process of the slurry. The specific requirement is to use a minimum amount of binder, add a reasonable amount of nano-scale alumina, surfactant and pH regulator to make the powder. The pulp achieves the desired viscosity, specific gravity and rheological properties. If the binder is used in a large amount, it is waste on the one hand, and on the other hand, the burden on the baking process is increased; if the amount of alumina is unreasonable, the initial luminous flux and lumen maintenance rate, the appearance of the coating, and the powder are affected. Adhesion strength; if the amount of surfactant is unreasonable, it affects the rheological properties of the coating liquid and the quality of the coating. In general, to understand the characteristics of the material, the coating liquid is formulated according to the characteristics of various materials to obtain a uniform, low-porosity phosphor coating. In addition to the quality of the powder layer, it is required that the amount of the powder tube coated with the same weight of the rare earth phosphor is more than that of the organic powder coating solution prepared by using the butyl acetate as the solvent. The number of powder tubes produced can be obtained to obtain greater economic benefits.
Powder coating and baking tube
The process of water slurry coating is very simple. For U-shaped glass tubes or straight tubular glass tubes, the perfusion method, the spraying method and the suction coating method can be used, as long as the air temperature and air volume of the blowing are controlled. The effect of the working temperature of the powder coating machine is not very large, as long as it is not very low (especially in winter). The reason is that the drying of the slip does not depend on the ambient temperature of the powder coating machine, but on the dry hot air blown in. It can be seen that the water slurry coating technology is not high on the powder coating machine. In fact, we cooperated with the factory to renovate the original powder coating machine with organic coating liquid coating (the whole chain transmission mechanism is 6m long and 3m long on one side), separating the two sides, plus a blowing pipe ( If you blow hot air, you can use this equipment to apply water slurry, and the coating effect is also very good. We believe that the preparation of the slurry is the key, and the powder coating machine is relatively minor.
Many people believe that since the decomposition temperature of the water-soluble binder is low, as long as the temperature of the lower tube is low. In fact, it is not so simple, because nitrocellulose and polyethylene oxide have their own characteristics: nitrocellulose breaks down quickly, runs away quickly by burning in oxygen, but requires higher temperature and sufficient oxygen; polyoxyethylene decomposes Slowly, decomposition starts at a temperature of about 2000 ° C. In order to make the decomposition reaction proceed smoothly, there is a certain requirement for the atmosphere. Therefore, we specifically determined the relationship between the decomposition weight loss of the polyethylene oxide binder and the temperature, time and blowing of the baking tube [5], which led to the best specification of the baking tube temperature.
Conclusion: For compact fluorescent tubes, in order to obtain high-quality rare earth fluorescent powder layer, a new water slurry coating process should be adopted; the preparation process of the slurry should be formulated according to the characteristics of the materials used; Formulated according to the thermal decomposition characteristics of polyethylene oxide.
Dc Gear Motor can be defined as an extension of Dc Motor which already had its Insight details demystified here. A dc Gear Motor has a gear assembly attached to the motor. The speed of motor is counted in terms of rotations of the shaft per minute and is termed as RPM .The gear assembly helps in increasing the torque and reducing the speed. Using the correct combination of gears in a dc gear motor, its speed can be reduced to any desirable figure. This concept where gears reduce the speed of the vehicle but increase its torque is known as gear reduction.
Application field: usually used Electronic door locks, shutter motor, home audio equipment, sweep the floor machine robot
Features: dc gear motor drive precision, small volume, large torque, low noise, durability, low energy consumption, customized power design,easy installation, easy maintenance;Simplify design and save space.
Method of use: the best stable in horizontal plane, installed on the dc gear motor output shaft parts, cannot use a hammer to knock,knock prone to press into the dc gear motor drive, may cause damage to internal components, and cannot be used in the case of blocked.
Operating temperature range:
Dc geared motors should be used at a temperature of -10~60℃.
The figures stated in the catalog specifications are based on use at ordinary room temperature catalog specifications re based on use at ordinary room temperature (approximately20~25℃.
If a geared motor is used outside the prescribed temperature range,the grease on the gearhead area will become unable to function normally and the motor will become unable to start.Depending on the temperature conditions ,it may be possible to deal with them by changing the grease of the motor's parts.Please feel free to consult with us about this.
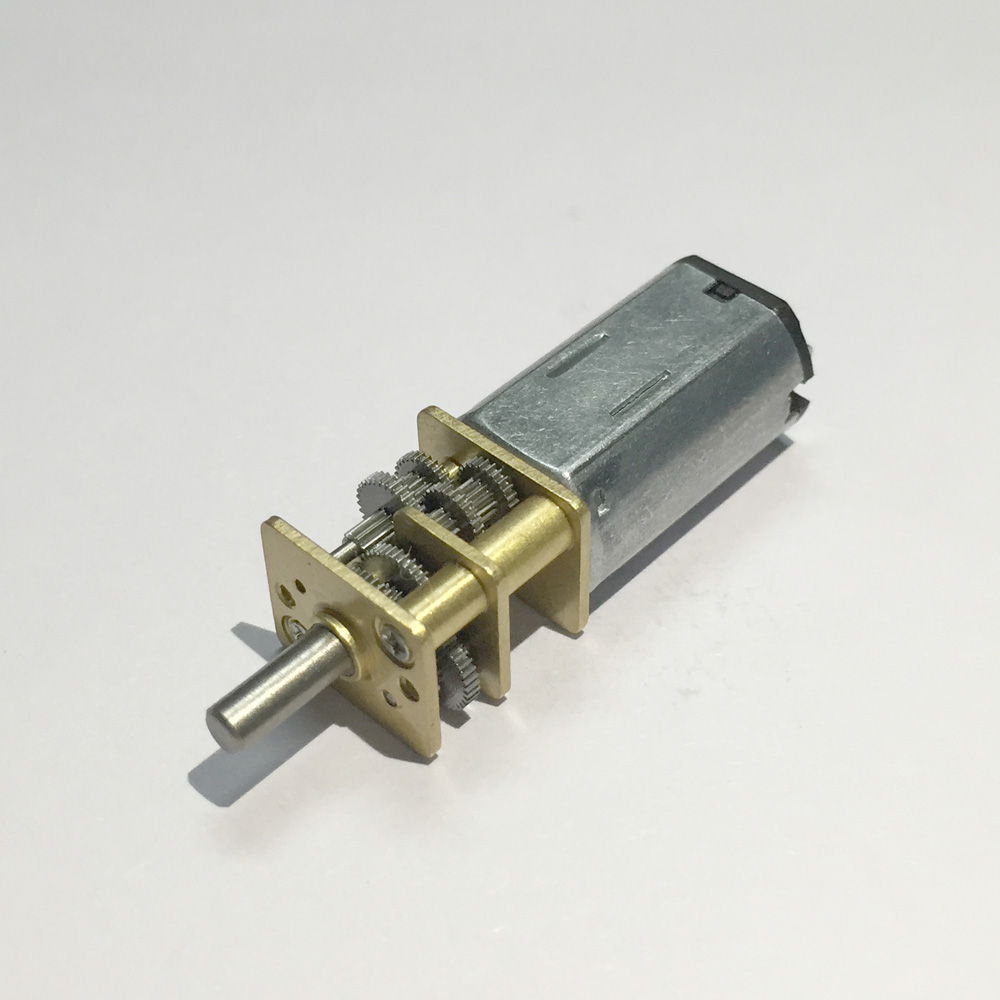
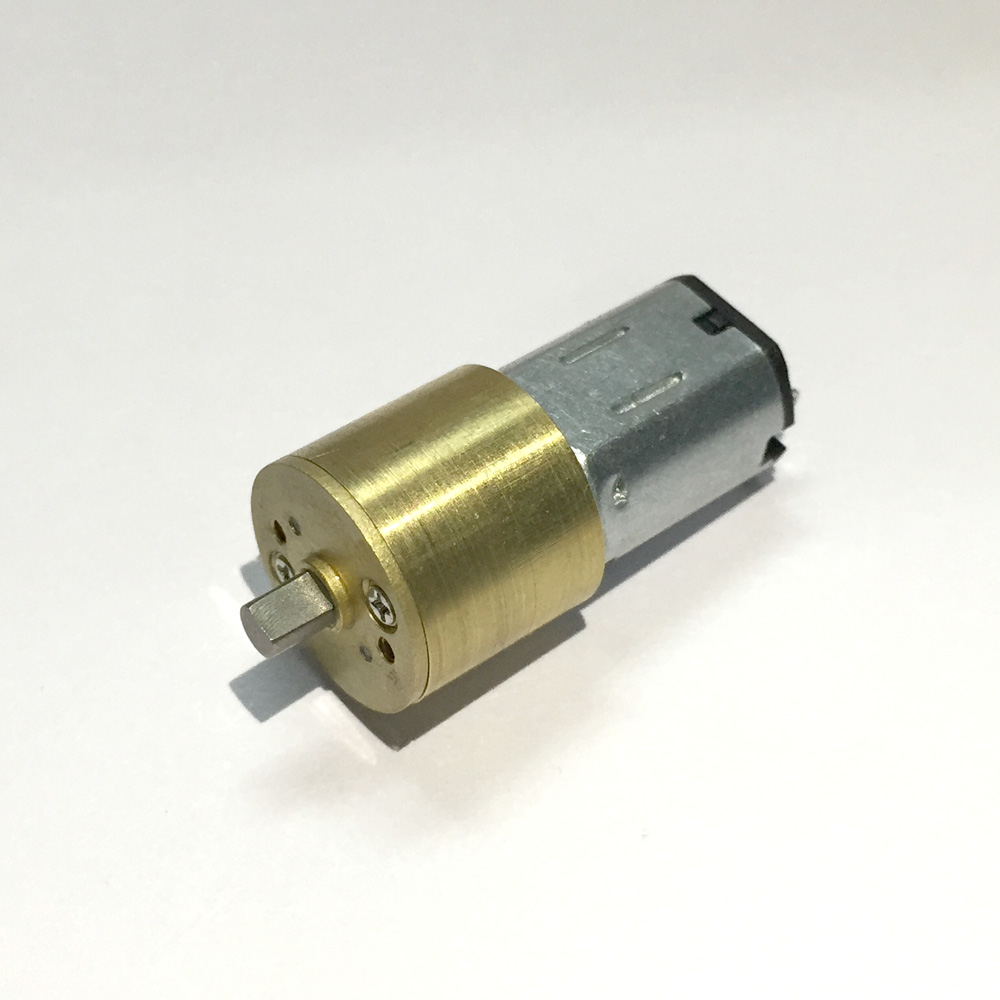
Storage temperature range:
Dc geared motors should be stored ta a temperature of -15~65℃.
In case of storage outside this range,the grease on the gearhead area will become unable to function normally and the motor will become unable to start.
Service life:
The longevity of dc gear motor is greatly affected by the load conditions , the mode of operation,the environment of use ,etc.Therefore,it is necessary to check the conditions under which the product will actually be used .The following conditions will have a negative effect on longevity.Please consult with us should any of them apply.â—Use with a load that exceeds the rated torque
â—Frequent starting
â—Momentary reversals of turning direction
â—Impact loads
â—Long-term continuous operation
â—Forced turning using the output shaft
â—Use in which the permitted overhang load or the permitted thrust load is exceeded
â—A pulse drive ,e.g.,a short break,counter electromotive force,PWM control
â—Use of a voltage that is nonstandard as regards the rated voltage
â—Use outside the prescribed temperature or relative-humidity range,or in a special environment.
â—Please consult with us about these or any other conditions of use that may apply,so that we can be sure that you select the most appropriate model.
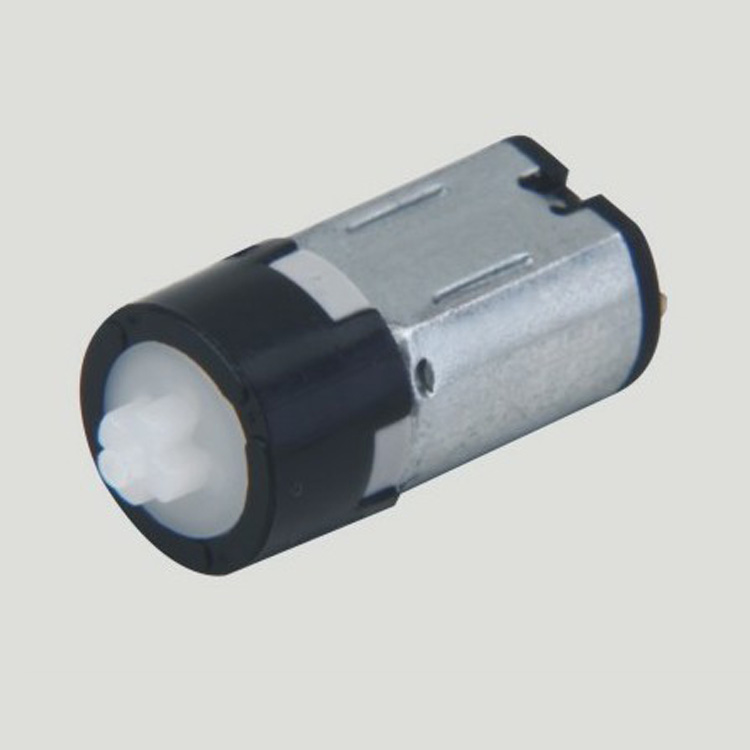
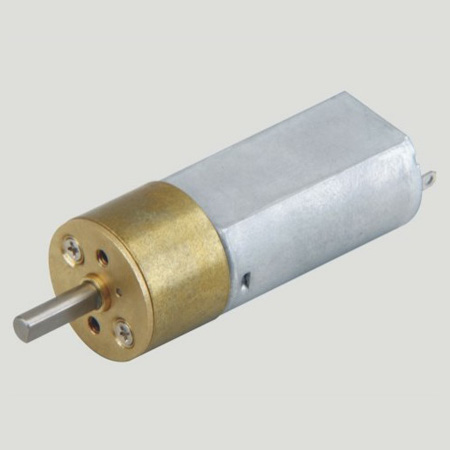
when it come to volume production,we're a major player as well .each month,we rurn out 600000 units,all of which are compliant with the rohs directive.Have any questions or special needed, please contact us, we have the engineer group and best sales department to service to you Looking forward to your inquiry. Welcome to our factory.
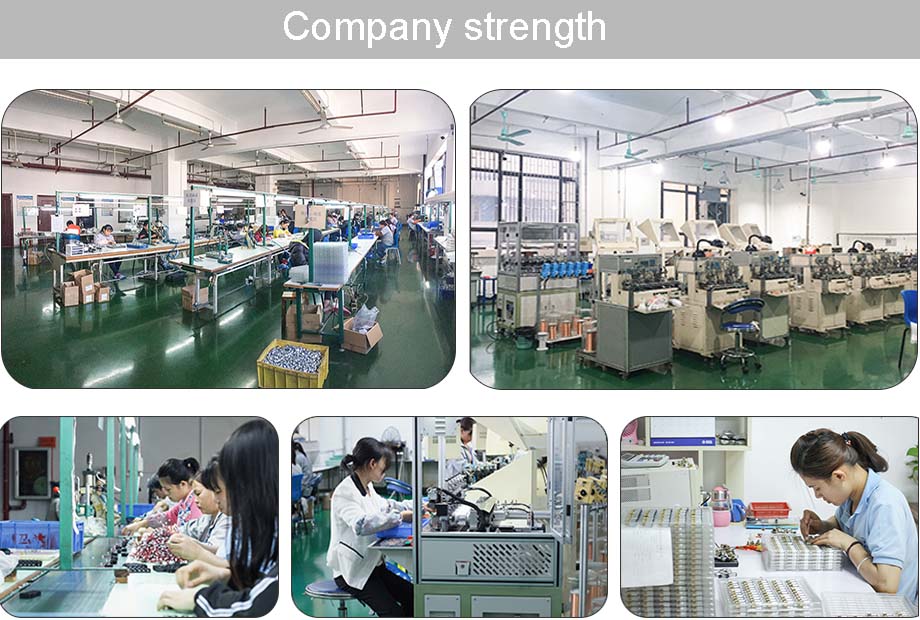
Dc Gear Motor
Dc Gear Motor,Gear Box Motor,Gear Reduction Motor,Small Diameter Dc Gear Motor
Shenzhen Shunchang Motor Co., LTD. , https://www.scgearmotor.com